Gases that are liquefied via very cold temperatures are known as cryogenic liquids. A cryogenic liquid may be referred to as a cryogen if it is used to cool other substances. The temperature at which a liquid is considered cryogenic varies by source, but it is generally below -150° F. The boiling point of a cryogenic liquid is the temperature at which it changes state from liquid to gas. This boiling temperature will vary for a given type of fluid (nitrogen, oxygen, helium, etc.) and pressure applied. A “phase diagram”, as shown in example Figure 1, depicts how a substance changes state from gas, to liquid, to solid for any given temperature and pressure combination. Boiling points are often tabulated for standard atmospheric pressure as reference points.
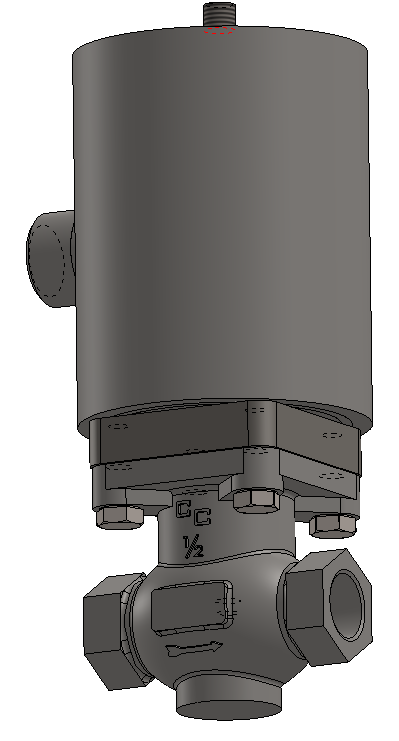
Cryogenic Solenoid Valve Example
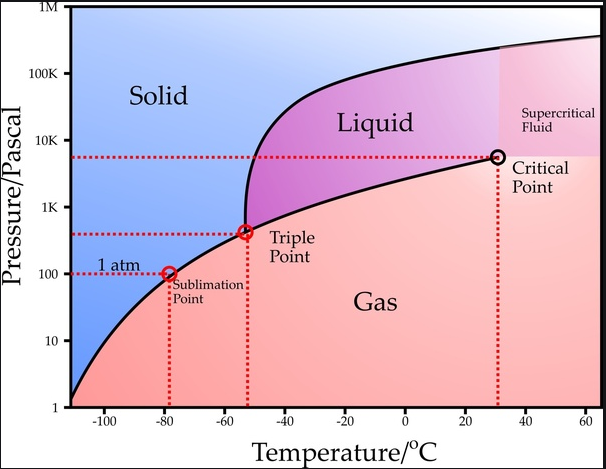
Solenoid Valves Control the Flow
Solenoid valves intended to control the flow of cryogenic liquids are specially designed for such low temperatures and possible state changes (gas and liquid).
Materials for construction must not become excessively brittle at cryogenic temperatures. Typical metals used for valve bodies, bonnet tubes, and fasteners are austenitic stainless steel, bronze, and monel. Carbon steels, plastics, and rubbers become too brittle at cryogenic temperatures and are therefore avoided. Polytetrafluoroethylene (PTFE), also known by the brand name Teflon, is a chemically inert synthetic fluoropolymer that works very well for valve discs. The valve disc is a moving wetted component inside a solenoid valve that interfaces with metal seats to seal off the working fluid. PTFE has a huge useable temperature range, no embrittlement, and can be designed deform just the right amount for a give valve seat. It can also be used as the filler in gaskets.
Inside a Valve
The moving components inside a solenoid valve will contract by several thousandths of an inch when exposed to a cryogenic liquid. The design must account for this to prevent lockup from such cold contraction and the possibility of ice formation.
Liquid Gas Expansion and Boiling Reference Points
Table 1 shows the aforementioned boiling reference points, as well as the liquid to gas expansion ratio. If a cryogenic liquid was trapped inside a sealed chamber and allowed to warm up to room temperature, pressure would skyrocket as the liquid boils and changes state from liquid to gas. As indicated by the expansion ratios, the gas volume would comparatively occupy hundreds of times more volume at standard temperature and pressure. Cryogenic systems therefore have built in relief valves, as shown on the picture below of the cryogenic nitrogen tank (350 psi max). Pertaining to solenoid valves, no sealed off compartments may exist inside the valve without a path to such a relief valve in the system, typically upstream.
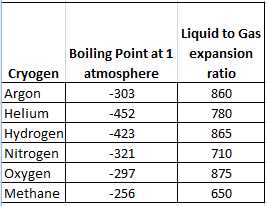
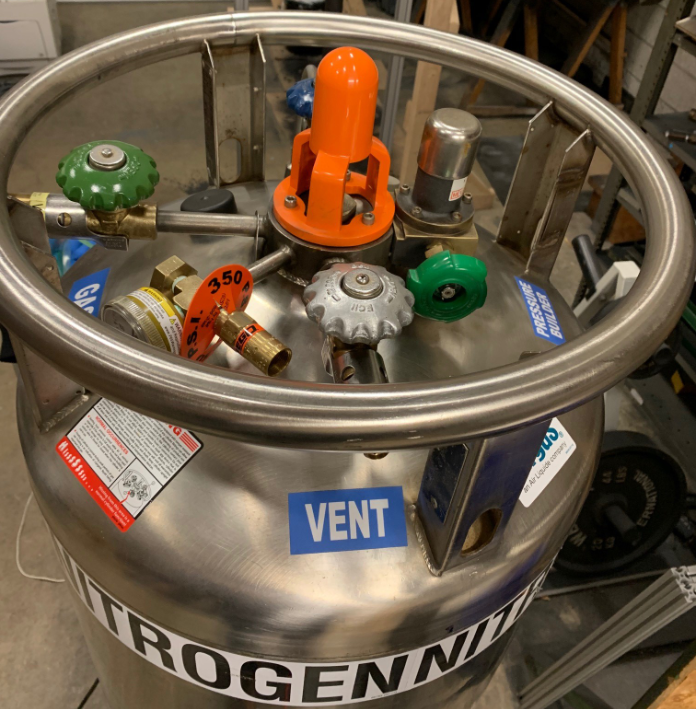
Optimize Performance for Gases and Liquids
Solenoid valves often have specifically sized pilot and bleed holes designed into the main pistons, which move to open and close a valve. These holes optimize performance for gases, liquids, and sometimes viscous liquids. A valve optimized for a gas might close too slowly if a liquid is run through it. A valve optimized for a liquid may actually not fully open for a gas. Cryogenic tubing and pipes may extend significant distances in an application and may be exposed to ambient temperature air. The large temperature difference adds heat energy to the cryogenic fluid, so it is possible for gas or gas/liquid mixtures to build up in the lines. The cryogenic solenoid valve must be able to operate for both liquids and gases. This phenomenon is important to understand for non-cryogenic temperatures as well. Liquid carbon dioxide can exist at 32°F with less than 800 psi. It can change state in the application piping without much heat addition and require the same “dual” gas and liquid functionality.
No Rubber O-Rings
Lastly, the inlet and outlet connection type should not utilize any rubber o-rings, therefore the common SAE J1926 connection should not be employed. NPT connections properly tightened with PTFE tape are sufficient for the majority of cryogenic pressure applications. Metal to metal would be a second option.
When selecting a solenoid valve for your cryogenic application, provide as much usage detail to the salesperson or engineer as possible for success.